
Concrete Pad & Strip Foundations: Essex Specialists
Engineered Foundation Solutions for Chelmsford Homes
Building on Solid Ground in Essex
WHY YOUR FOUNDATION CHOICE MATTERS
The foundation isn't just another construction element—it's quite literally what everything else depends on. At Construction Inc Limited, your trusted Builders Chelmsford, we've spent over a decade perfecting our approach to concrete pad foundations and strip foundation installations across Essex's challenging soil conditions. While the foundation itself remains unseen once your project is complete, its quality determines whether your extension stands strong for generations or develops problems within years. Our precision-engineered foundations are designed specifically for local soil conditions, with calculations that account for Essex's notorious clay shrinkage potential, proximity to trees, and variable water tables—factors that generic builders often overlook.
We understand that foundation work seems daunting—excavation equipment rumbling through your garden, trenches appearing where your patio once stood. That's why our family-run team emphasizes careful site protection and clean working practices throughout the process. Your dedicated project manager coordinates every aspect, from arranging building control inspections to scheduling concrete deliveries at times that minimise disruption to your household. For a comprehensive overview of our groundworks capabilities, explore our main groundworks page. Have questions about foundation types, timelines, or budget considerations? Our FAQ page covers common concerns. Ready to discuss your specific foundation requirements? Contact us today for a free, no-obligation site assessment.
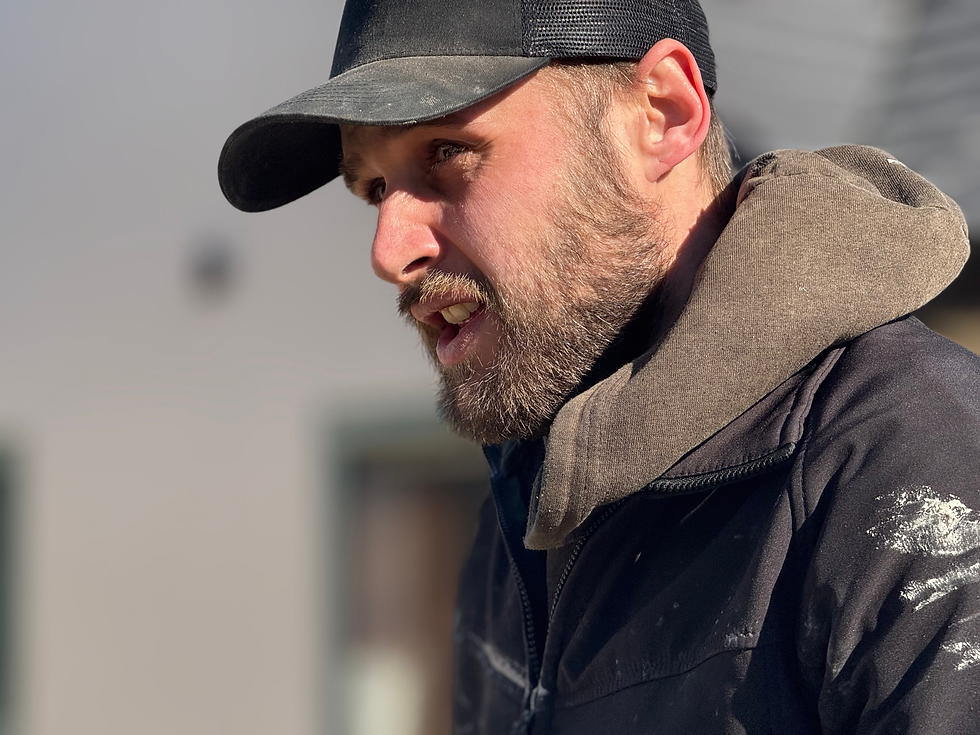
Selecting the Right Foundation for Your Project
MATCHING FOUNDATIONS TO ESSEX SOIL CONDITIONS
Choosing among various foundation types for houses requires careful consideration of your specific site conditions and building plans. Concrete pad foundations provide exceptional load-bearing capacity for concentrated weights, making them ideal for supporting structural columns, heavy chimney breasts, or conservatory corner posts. Typically measuring 600mm × 600mm square and 200-300mm deep, these individual pads distribute loads effectively while using less concrete than continuous foundations. By contrast, traditional strip foundations create a continuous bearing surface beneath load-bearing walls, typically 450-750mm wide depending on soil conditions and wall thickness. For Essex properties with moderately stable ground, trench fill foundations—deeper, narrower strips poured directly against soil walls—often provide a cost-effective alternative that eliminates the need for traditional brick footings.
The geology beneath your property significantly influences foundation selection. In areas of Chelmsford with shrinkable clay (common throughout central Essex), foundations typically require greater depth—usually 1000-1500mm—to reach below the zone affected by seasonal moisture changes. Properties near mature trees require even deeper foundations due to root-induced soil desiccation. Conversely, areas with sandy or gravelly soils might permit shallower foundations of 750-900mm. Rather than applying a one-size-fits-all approach, we conduct thorough site investigations before recommending specific foundation specifications. For a deeper understanding of how soil conditions affect foundation design, visit our comprehensive guide to Foundation Solutions for Residential Properties. Each foundation type offers distinct advantages depending on your specific circumstances and building plans.
The Strip Foundation Construction Process
FROM EXCAVATION TO CONCRETE POURING
Professional strip foundation construction follows a methodical process that begins long before any concrete is poured. Our approach starts with precise setting out using laser levels to establish accurate lines and levels—typically working to tolerances of ±5mm. Excavation then proceeds to the specified foundation depth, with trenches cut 150-200mm wider than the designed foundation width to allow working room. For typical domestic extensions in Chelmsford, we excavate to at least 1000mm depth to exceed the minimum building regulation requirement of 750mm, providing extra protection against ground movement. Once excavated, trenches are inspected for consistent soil bearing capacity, with any soft spots removed and replaced with compacted hardcore. Before the building control inspection, we install steel reinforcement—typically A393 mesh for standard applications, supplemented with 12mm steel bars at stress points.
The concrete mix specification is critical to foundation performance. We use C25/30 concrete grade with 20mm aggregate as standard for strip foundation construction—a step above the C20 often used by less diligent builders. This higher-strength mixture provides significantly improved durability and crack resistance. For challenging ground conditions, we may specify sulphate-resistant cement to counter chemical attack from certain clay soils common in parts of Essex. The concrete footing is poured in a single operation where possible to avoid cold joints, with careful vibration to eliminate air pockets that would compromise strength. After pouring, we protect the concrete from rapid drying or frost depending on weather conditions, ensuring proper concrete curing. For more information about our site preparation process leading up to foundation construction, visit our detailed Site Preparation and Excavation Services page. Our attention to detail during each stage ensures foundations that exceed building regulation requirements.

Engineering Stronger Foundations Through Reinforcement
STEEL REINFORCEMENT TECHNIQUES FOR DURABILITY
While concrete exhibits exceptional compressive strength, it performs poorly under tension—which is why professional reinforced concrete foundations incorporate carefully designed steel elements. The reinforcement configuration depends on the specific loads and soil conditions, but typically includes A393 mesh (10mm bars at 200mm centres) providing bidirectional strength. For foundations supporting heavier structures or spanning areas of variable ground conditions, we incorporate additional 12mm or 16mm high-yield steel bars at calculated positions. This reinforcement particularly matters in Essex, where the shrinkable clay soils can exert significant seasonal pressure on foundations. Without proper reinforcement, even minor ground movement can cause foundation cracking and subsequent structural issues that might not become apparent for several years.
The placement of reinforcement within the concrete is as important as the reinforcement itself. We maintain precise positioning using plastic spacers to ensure the steel sits 50-75mm above the trench bottom and at least 50mm from any edge—guaranteeing proper concrete coverage to prevent corrosion. For step foundations on sloping sites, we extend reinforcement across steps to prevent differential settlement. All steel is secured with proper overlap joints (typically 300-600mm depending on bar diameter) and tied with galvanised wire to prevent displacement during concrete pouring. We also incorporate starter bars where foundations will connect to ground beams or slab edges, creating a monolithic structure that distributes loads more effectively. These detailed foundation specifications ensure our reinforced concrete foundations deliver decade after decade of reliable performance. For further information on how proper foundations contribute to structural integrity, see our page on Foundation Solutions for Residential Properties.
Professional Concrete Slab Installation
CREATING PERFECT LEVEL SURFACES FOR BUILDING
Professional concrete slab installation requires far more preparation than simply pouring concrete onto the ground. We begin by excavating to the required depth—typically 250-300mm below finished floor level—then install a capillary break layer of 50-75mm clean stone to prevent ground moisture migration. Above this, we place 100mm of compacted hardcore (MOT Type 1) in two layers, each compacted with a vibrating plate to achieve 95% modified Proctor density. This sub-base preparation is critical for preventing future settlement. We then install 1200-gauge damp proof membrane, carefully lapped at joints and turned up at edges to form a continuous moisture barrier. For thermal performance, we lay 75-100mm XPS insulation boards (typically 300kPa compressive strength) with staggered joints to eliminate thermal bridging.
The concrete mix for quality concrete slab installation typically uses C25/30 concrete grade with plasticizer for workability without excessive water that would compromise strength. For residential floor slabs, we incorporate polypropylene fibres at 0.9kg/m³ to control microscopic cracking during concrete curing. Once poured to a minimum thickness of 100mm (often 150mm for garages or outbuildings), we use power floats to create a perfectly level, smooth surface with a tolerance of ±3mm across 3 meters. Proper concrete curing is ensured by applying membrane curing compound and protecting the slab from rapid drying for at least 7 days. This methodical approach creates slabs that remain crack-free and level for decades. For more information about our comprehensive concrete services, visit our detailed page on Concrete Foundations: Pad and Strip Options.

The Long-Term Value of Professional Foundation Work
INVESTMENT PROTECTION THROUGH QUALITY FOUNDATIONS
While proper concrete pad foundations might represent 8-12% of your total construction budget, they deliver disproportionate value in terms of structural integrity and long-term performance. Foundation issues typically cost 3-5 times more to rectify than to prevent—with repair work often involving disruptive underpinning that can exceed £30,000 for modest properties. Professional foundation work also significantly impacts resale value, with surveyors specifically examining foundation quality during pre-purchase surveys. Problems identified at this stage can substantially reduce property valuation or even prevent mortgage approval. Our foundations are designed and constructed to exceed building regulations, providing documentation that offers valuable reassurance for future buyers of your property.
Beyond structural integrity, quality foundations contribute to overall building performance. Properly insulated concrete slab installation reduces heat loss through ground contact, potentially saving 8-12% on annual heating costs. Precision-levelled foundations ensure trouble-free installation of kitchens, flooring, and other finishes—eliminating the expensive corrections often needed when building on substandard foundations. Most importantly, they provide decades of trouble-free service without the telltale signs of settlement: sticking doors, cracked plasterwork, and uneven floors. At Construction Inc Limited, we don't just meet minimum standards—we build foundations designed for generational performance. For detailed information about project costs and budgeting for foundation work, visit our comprehensive Groundworks Cost Guide and Budgeting page. Ready to discuss your foundation requirements? Contact us today for expert advice and a detailed quotation.